18.08.2020
Materialfluss neu organisiert
Der tschechische Landmaschinenhersteller Bednar FMT hat ein neues Montagewerk in Betrieb genommen und in dem Zug auch ein neues Produktionskonzept verwirklicht. Jetzt können sowohl kleinere als auch sehr große Landmaschinen auf einer Linie produziert werden. Möglich wird dies durch eine Dreiteilung des Montageprozesses – und durch insgesamt 19 Krane mit je zwei Hubwerken und zwei KBK-Systemen.
Im Landmaschinenbau gibt es viele „Big Player“, die auf mehr als hundert Jahre Firmengeschichte zurückblicken können. Die 1997 in Tschechien gegründete Bednar FMT s.r.o. ist dazu im Vergleich ein echter Newcomer. Ein sehr erfolgreicher Newcomer. Das Unternehmen bietet den Landwirten ein breites Portfolio von gezogenen Landmaschinen, wie Sämaschinen, Drillmaschinen, Kurzscheibeneggen und Reihenkultivatoren. Bednar exportiert rund 90 Prozent seiner Produktion in 35 Länder – ein Zeichen, dass die Maschinen dem Landwirt auch heutzutage echten Mehrwert bieten.
Neues Montagewerk mitflexiblem Produktionskonzept
Wachstum braucht Produktionskapazitäten: Deshalb hat Bednar im März 2020 ein neues Montagewerk in Rychnov nad Kněžnou in Betrieb genommen. Auf zwei Etagen steht eine Fläche für Produktion und Versand von rund 10.000 Quadratmetern zur Verfügung.
Die – im Vergleich zur alten Montage – Verdoppelung der Fläche schaffte die Voraussetzung dafür, dass Bednar ein neues Montagekonzept verwirklichen konnte. Dabei galt es, eine besondere Herausforderung zu meistern. Ing. Vojtěch Bednář, geschäftsführender Gesellschafter des Unternehmens: „Unsere Maschinen sind zumeist modular aufgebaut. Das Programm umfasst sehr kompakte Maschinen mit Arbeitsbreiten von etwa drei Metern und auch solche, die mit einer Arbeitsbreite von 16 bis 18 Metern übers Feld fahren. Entsprechend flexibel muss vor allem die Endmontage sein: Kleine und sehr große Maschinen müssen sich effizient montieren lassen – auf ein und derselben Linie.“
Landmaschinenmontagein drei Schritten
Das neue Montagekonzept ist dreistufig aufgebaut. Im Obergeschoss findet die Vormontage statt: Unterbaugruppen der Maschine werden zu Modulen kombiniert. Hier sind Gewichte von 15 bis 500 Kilogramm zu handhaben. Teilweise werden die Module dann lackiert. In jedem Fall werden sie über Vertikalförderer ins Untergeschoss gefördert, wo zunächst der zweite Produktionsschritt erfolgt: die Montage der Unterbaugruppen, die bis zu 2.000 Kilogramm wiegen können.
Komplettiert werden die bis zu zehn Tonnen schweren Maschinen dann im dritten Schritt, der Endmontage. Das dreistufige Konzept hat letztlich das Ziel, die Endmontage zu entlasten. Aus Sicht der Intralogistik heißt das: Es mussten Krane und Handhabungslösungen für drei verschiedene Gewichtsklassen ausgewählt werden. Vojtěch Bednář: „Mit unserer neuen Montagelinie haben wir ein Fertigungskonzept umgesetzt, mit dem wir sowohl kleinere Serien und zugleich eine hohe Varianz abdecken können.“
In Kooperation mit Demag Tschechien – und nach einem Besuch des Demag-Werkes in Slany – entschied sich Bednar für ein Materialflusskonzept, das auf 19 Demag-Laufkranen vom Typ EKKE mit jeweils zwei Laufkatzen (Tragfähigkeit: 2 x 3,2 Tonnen und 2 x 5 Tonnen) basiert.
Sechs der größeren Krane haben ein Spurmittenmaß von 18,60 Meter, acht Krane überspannen 13,45 Meter. Sie sind jeweils in einer Linie angeordnet, so dass die zu montierenden Teile von einer Station zur nächsten transportiert werden können. Die letzten Krananlagen in dieser Prozesslinie sind im Versand installiert, wo die fertigen Landmaschinen auf Lkw verladen werden.
Vojtěch Bednář: „Für die Mitarbeiter im Versand, die bislang auf ältere Krane zugreifen mussten, stellt die neue Krantechnik eine sehr große Veränderung zum Guten dar. Die Kranfunktionen, wie die Wiegeeinrichtung, der Tandembetrieb sowie die Steuerung von vier Katzen, machen die Verladeprozesse erheblich effizienter und sicherer.“
Die kleineren Krane mit 2 x 3,2 Tonnen Tragfähigkeit und einem Spurmittenmaß von 13,55 Metern kommen in der Vormontage zum Einsatz.
KBK-Anlagen fürergonomische Montagearbeiten
Außerdem nutzt das Bednar-Personal im neuen Werk zwei 62 Meter lange KBK-Krananlagen mit jeweils fünf Hängekranen und Kettenzügen DC (Tragfähigkeit: 1.000 Kilogramm). Bei diesem System verfahren an einem Trägersystem Leichtlaufkrane, die der Bediener mit geringem Kraftaufwand und entsprechend geringer körperlicher Belastung führen kann.
Die eine Anlage „begleitet“ quasi die Vormontage. Sie überspannt die Montageplätze, die sich hier parallel zur Kranlinie befinden, und erleichtert das Montieren, Handhaben und Bereitstellen kleinerer Komponenten. Die andere Anlage ist im Umfeld der Lackiererei installiert und erlaubt den ebenso flexiblen wie geordneten Durchlauf (mit Pufferzonen) der zu lackierenden Teile.
Fazit: Ein durch und durch schlüssiges Konzept
Damit hat Bednar ein praxisgerechtes und abgestuftes Materialflusskonzept aus einer Hand – von Demag – realisiert, mit dem sowohl Kompaktmaschinen als auch Landmaschinen mit Arbeitsbreiten von 18 Metern und mehr flexibel und effizient auf einer Linie produziert werden können.
Vojtěch Bednář: „Im alten Werk war das unser Bottleneck, in dem sehr viele Montageschritte zu erledigen waren. Jetzt ist der Prozess sehr gut strukturiert, weil wir einen Teil der Prozesse von der Hauptlinie ausgelagert haben und individuelle, zeitraubende Montageprozesse abtrennen. So können wir in der Endmontagelinie besser atmen und wir sind dadurch auch wesentlich flexibler geworden.“
Keine Wartezeit:Arbeitsplatz – ein Hebezeug
Ein weiterer Grund für die erhöhte Produktivität ist die Tatsache, dass jeder Arbeitsplatz in jeder Linie mit einer eigenen Hublösung ausgestattet ist. So sparen die Werker die Wartezeit auf einen freien Kran.
Neben der Flexibilität und der verkürzten Durchlaufzeit war für Bednar auch die Ergonomie ein wichtiger Planungsaspekt. Vojtěch Bednář: „Wir möchten dem Personal die Arbeit erleichtern – mit durchdachten Arbeitsplätzen, guter Beleuchtung und auch mit Hebezeugen, die optimal auf den jeweiligen Arbeitsprozess abgestimmt sind. Da haben wir mit den Kranen und vor allem mit dem KBK-System einen großen Schritt nach vorn gemacht.“
Nicht zu unterschätzen ist auch der Aspekt des schonenden Handlings: Die schweren Komponenten müssen mit großer Präzision montiert werden, um ein tadelloses Aussehen und alle Funktionen zu gewährleisten.
Und da Bednar kontinuierlich wächst, spielte bei der Planung auch die Skalierbarkeit der Handhabungstechnik eine zentrale Rolle. Das Produktions- und Materialflusskonzept mit Kranen und KBK-Systemen ist so flexibel ausgelegt, dass es zum Beispiel auch bei kürzeren Durchlaufzeiten einwandfrei funktioniert.
Sorgfältige Auswahl des Kranherstellers
Die Auswahl des Kranherstellers haben sich die Verantwortlichen nicht leicht gemacht. Vojtěch Bednář: „Schließlich ist die Montage völlig abhängig von den Kranen. Wir wussten ziemlich genau, was wir wollten, haben das Angebot der Kranhersteller studiert und auch mehrere Werke und Referenzprojekte besucht. Die Servicequalität spielte ebenfalls eine Rolle. Was uns bei Demag überzeugt hat, waren die Referenzprojekte, die Qualität der Krane, der leistungsfähige Service und auch die persönliche Unterstützung bei der Projektierung.“
Bislang wurden die Erwartungen erfüllt: „Zur dauerhaften Qualität von Anlagen wie Kranen lässt sich erst nach mehreren Jahren eine Aussage treffen. Aber ich kann die bisherige Zusammenarbeit bewerten: Die Liefertermine, die gesamte Installation, die Inbetriebnahme, der technische Support – all das ist ohne jedes Problem verlaufen. In dieser Hinsicht sind wir zufrieden, und das neue Konzept bewährt sich in der Praxis.“
Ergebnis einer vetrauensvollen Kooperation
Jirí Herian, Direktor Vertrieb, Demag Krane Tschechien, ergänzt: „Dieses Vorzeigeprojekt ist das Ergebnis einer jahrelangen, vertrauensvollen Kooperation zwischen Bednar FMT und Demag. Begonnen hat diese Kooperation mit einigen kleineren Projekten und wir sind sehr glücklich darüber, dass Bednar FMT uns auch bei diesem großen Projekt als Partner ausgewählt hat.“
„Die Planung und Umsetzung eines anspruchsvollen Intralogistik-Konzepts für die moderne Fertigung in Rychnov nad Kněžnou sowie die stetige Unterstützung unseres Kunden“, so Herian weiter, „erfordern eine hohe Anforderung, die unser Vertriebsingenieur Martin Bednár fantastisch umgesetzt hat. Wir freuen uns sehr darauf auch in Zukunft Bednar FMT mit unserem Service und unserer Expertise unterstützen zu dürfen.“
(jak)
Von Redaktion (allg.)
veröffentlich vonTechnische Logistik
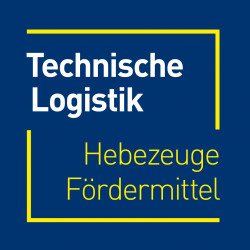