08.10.2020
Innovative Parallelkinematik ersetzt Roboter
Die Anforderungen an Maschinen und Anlagen in der Intralogistik steigen. Dazu zählen hohe Produktionsgeschwindigkeit und Präzision, schnelle Produkt- und Formatwechsel sowie immer kleinere Losgrößen. Insbesondere beim Produkthandling besteht Verbesserungspotenzial. Abhilfe schaffen modular kombinierbare Maschinen und Gesamtanlagen mit einem intelligenten Automatisierungssystem.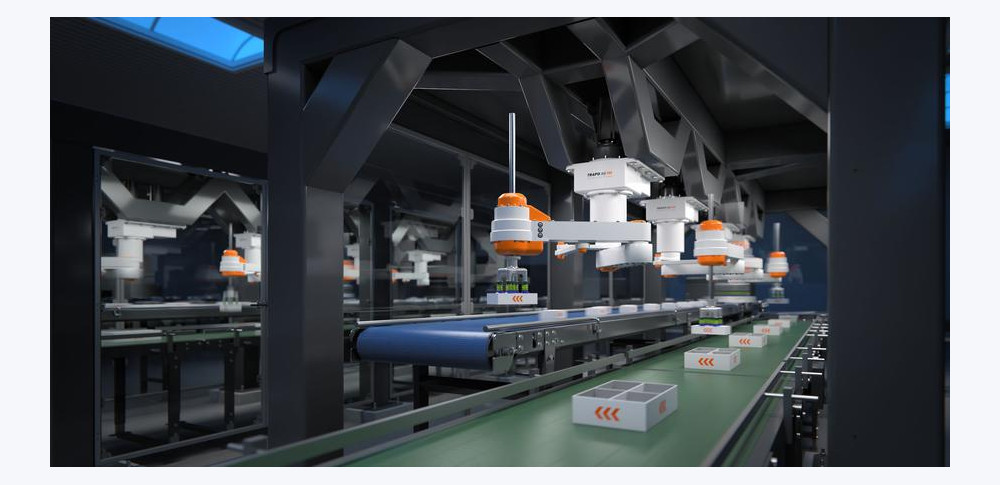
Als Pionier entwickelte die Trago AG, Partner für industrielle Automatisierung, gemeinsam mit Forschungseinrichtungen der RWTH Aachen eine ebene Hochleistungsparallelkinematik. Sie kann bei Verpackungsprozessen den traditionell von Drittanbietern stammenden Knickarmroboter ersetzen und übernimmt Aufgabenstellungen, die hohe Präzision und Leistung erfordern.
Parallelkinematik sorgt für Flexibilität und Präzision
Die Hochleistungsparallelkinematik besteht aus einer fünfgliedrigen kinematischen Struktur, einer Z-Achse und einem Drehmodul zur Orientierung. Das modulare System besitzt optional drei oder vier Freiheitsgrade und kann als Highspeed-Pick-and-Place-System (HPPS) als Pickervariante Produkte mit bis zu 200 Teilen pro Minute und Payload bis zu einem Kilogramm sowie als Highspeed-Kinematik-System (HKS) mit bis zu 60 Teilen pro Minute und Payload bis zu fünf Kilogramm. Für Anwendungen als Packroboter wird die vierte Z-Achse benötigt, um zugeführte Produkte zu greifen und beispielsweise in einen Karton zu verpacken. Mithilfe einer Kamera erkennt die Parallelkinematik die Lage der Teile. Diese werden anschließend gepickt oder im NIO-Fall ausgeschleust.
Um ihn für den Anwendungsfall zu optimieren, kann das innovative HPPS in verschiedenen Varianten gebaut werden: Bei der Variante mit großem Aktionsradius besitzt der Picker dank des parallelkinematischen Aufbaus einen rotationssymmetrischen Arbeitsraum und kann daher auch hinter sich greifen. Zudem ist der Parallelkinematik-Picker mit zwei Hüben (200 Millimeter und 400 Millimeter) erhältlich. Bei hoher Geschwindigkeit bietet er somit einen enormen Arbeitsraum. Auch die individuellen Greifer werden exakt an die Objekteigenschaften angepasst – und in der hauseigenen Forschung- und Entwicklungsabteilung, dem Trapo-Technikum, entwickelt und erprobt.
Von Redaktion (allg.)
veröffentlich vonTechnische Logistik
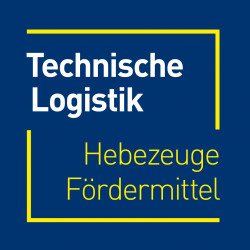